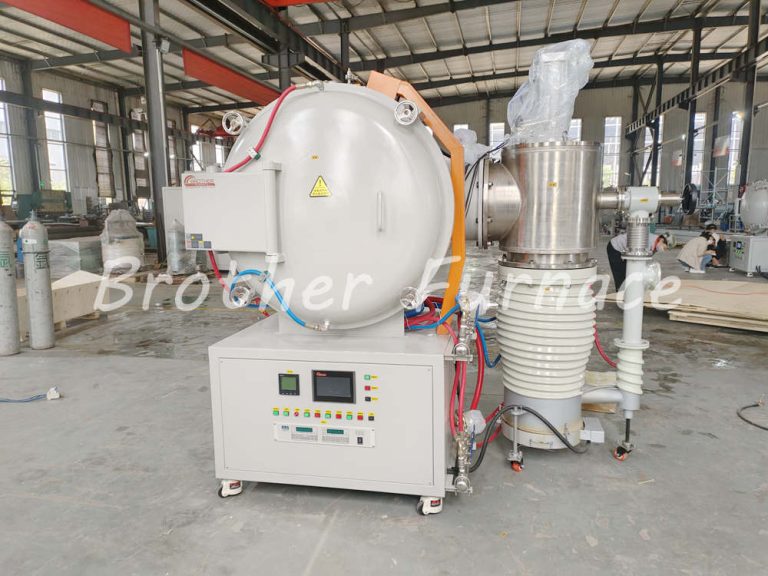
Vacuum box furnaces are essential in industries and research settings where precise thermal processing in oxygen-free or controlled environments is required. These furnaces are designed to accommodate a wide range of vacuum levels, from low to high, enabling diverse applications such as material synthesis, heat treatment, and advanced manufacturing. Below, we explore the distinct features, configurations, and applications of low-vacuum and high-vacuum box furnaces, leveraging insights from advanced furnace technologies outlined in related documents.
Low-Vacuum Box Furnace
Low-vacuum systems typically operate in the pressure range of 1000 Pa to 0.1 Pa, achieved using mechanical pumping systems. These furnaces balance cost-effectiveness with sufficient environmental control for many industrial processes.
Key Features:
- Vacuum System:
- Primarily relies on rotary vane or scroll pumps to achieve base vacuum levels.
- Suitable for applications requiring moderate gas evacuation, such as removing residual oxygen to prevent oxidation during annealing.
- Chamber Design:
- Constructed with stainless steel chambers for durability under moderate temperatures (up to 1200°C).
- Simplified sealing mechanisms (e.g., rubber gaskets) reduce costs but limit ultimate vacuum levels.
- Heating Elements:
- Heating wires are common for temperatures ≤1200°C.
- Uniform heating is ensured through single-zone configurations, ideal for bulk processing of metals or ceramics.
- Applications:
- Brazing and Sintering: Low-vacuum environments minimize oxidation while maintaining process efficiency.
- Pre-treatment of Additive Manufacturing Parts: Removing binders or degassing 3D-printed components.
- Glass-to-Metal Sealing: Ensuring hermetic joins in electronic packaging.
Advantages:
- Lower initial investment and maintenance costs.
- Faster pump-down times compared to high-vacuum systems.
- Adequate for processes where high purity is not critical.
High-Vacuum Box Furnace
High-vacuum furnaces operate at pressures below 0.1 Pa, often reaching 10⁻⁴ Pa or lower. These systems employ advanced pumping technologies and robust designs to achieve contamination-free environments, critical for sensitive applications.
Key Features:
- Pumping System:
- Combines mechanical pumps (for rough vacuum) with diffusion pumps, turbo-molecular pumps, or cryogenic pumps for high vacuum.
- Leak-proof seals (e.g., metal gaskets) and vacuum-rated flanges ensure long-term integrity.
- Chamber Design:
- Molybdenum-lined or Inconel chambers withstand extreme temperatures (up to 2200°C) and reactive atmospheres.
- Water-cooled jackets maintain safe external temperatures, even during prolonged high-heat cycles.
- Heating Elements:
- Graphite or tungsten elements enable high temperatures (≥1800°C) for specialized processes.
- Multi-zone heating configurations ensure precision in applications like crystal growth or semiconductor doping.
- Advanced Control Systems:
- Programmable logic controllers (PLCs) with multi-segment recipes for automated temperature ramps and dwell times.
- Real-time vacuum monitoring via ionization gauges or mass spectrometers, integrated with safety interlocks.
- Applications:
- Semiconductor Manufacturing: Annealing silicon wafers or depositing thin films via CVD (Chemical Vapor Deposition).
Advanced Ceramics: Sintering high-purity ceramics for aerospace or medical implants.
HIP (Hot Isostatic Pressing): Eliminating porosity in critical metal components under high vacuum and temperature.
- Semiconductor Manufacturing: Annealing silicon wafers or depositing thin films via CVD (Chemical Vapor Deposition).
Advantages:
- Eliminates trace contaminants, enabling high-pure material synthesis.
- Supports processes requiring precise atmosphere control (e.g., H₂ reduction).
- Enhanced thermal uniformity for high-value research and production.
Choosing Between Low and High Vacuum
The decision depends on process requirements and budgetary constraints:
- Low-vacuum furnaces are ideal for cost-sensitive, high-throughput operations where minor residual gases are acceptable.
- High-vacuum systems are indispensable for R&D, semiconductor fabrication, or any application demanding pristine environments.
Modern vacuum box furnaces often offer modular designs, allowing upgrades from low to high vacuum as needs evolve. By integrating features like programmable controls, multi-gas compatibility, and rapid cooling (via gas quenching), these systems bridge the gap between laboratory innovation and industrial scalability.
Conclusion
Vacuum box furnaces are versatile tools that cater to a spectrum of thermal processing needs. Low-vacuum configurations provide accessibility and efficiency for routine tasks, while high-vacuum systems unlock unparalleled precision for cutting-edge applications. As industries advance toward more stringent material standards, the ability to tailor vacuum levels and thermal profiles will remain pivotal in driving technological breakthroughs.
Contact us now for a custom quote or free design consultation.
Vacuum furnaces recommend :
- Vacuum Brazing Furnace
- Vacuum Sintering Furnace up to 1700℃
- Vacuum Induction Melting Furnace
- Graphite Vacuum Furnace up to 2200℃
- Vacuum Gas Quenching Furnace
- Vacuum Hot Press Furnace
Follow us on Facebook